激光隐切:半导体制造的一把利器
在半导体芯片制造过程中,需要采用切割工艺对晶圆进行划片,然而传统的金刚石切割、砂轮切割会对半导体材料造成较为严重的损伤,导致半导体晶圆碎裂、芯片性能下降等问题,因此开发出先进的切割技术将对集成电路半导体领域的降本增效具有极其重要的意义。随着激光技术的进步,采用高功率激光实现的激光烧蚀切割(即激光划片)和利用小功率激光聚焦实现的激光隐形切割(即激光隐切)技术逐渐成为了主流的芯片切割技术。激光切割技术属于非接触式加工方法,相对传统金刚石切割和砂轮切割,不会产生崩刃、刀具磨损和水污染,热影响和夹渣等不可忽视的问题。然而,激光烧蚀切割所采用的大功率激光在工作过程中会产生较高的热效应,因此在切割晶圆时容易同时破坏底部的蓝膜,进而对芯片加工工艺产生影响,因此激光隐切技术逐渐成为了半导体制造产业的关注焦点。
图1 晶圆切割技术:(a)金刚石刀片切割,(b)砂轮切割和(c)激光隐切技术
先进切割:激光隐切工艺详解及其应用举例
激光隐切技术通过将激光聚焦形成小面积的光斑,可产生巨大的能量密度,进而实现晶圆切割。作为一种干式工艺,激光隐切具有高速、高质量(无碎屑或极少碎屑)和低切口损失等优势。激光隐切的具体工艺过程可分为两个步骤:(1)激光诱导穿孔:如图2所示,采用光学系统将可透过晶圆的脉冲激光束聚焦到晶圆表面下方的焦点,当该焦点处激光功率密度达到峰值时,将会形成穿孔,此时晶圆上的芯片还未产生分离;(2)芯片分离:将放置在晶圆的蓝膜展开后,由于激光穿孔附近存在较大的张应力和压应力,因此可沿着激光路径在晶圆内部诱导产生裂缝,实现芯片分离。
图2 激光聚焦后在隐切层中形成穿孔
激光隐切技术目前已在多种晶圆切割上实现应用,例如:
(1)硅片切割:采用传统的金刚石刀片切割硅片时,刀片的厚度、粒度、旋转及切割速度会严重影响硅片切割的质量,尽管多年来人们一直在改进相关的技术方案,但刀片造成的大切割宽度(切口)仍然会导致材料的浪费,并且碎屑的产生及刀片磨损也增加了切割成本,而采用具有超窄切割路径的激光隐切技术,就可以避免额外的碎屑清理和材料浪费带来的成本问题,进而提高芯片的生产率,此外由于避免了热损伤问题,激光隐切技术还能够进一步提高芯片制造的良率;
(2)碳化硅切割:碳化硅是一种硬度仅次于金刚石的超硬材料,机械加工难度非常高,在大尺寸(6英寸及以上)碳化硅晶体衬底材料的制备环节,激光隐切技术相较于固定磨料(钻石电镀于钢线上)的线切割技术,其切割效率可提升3~5倍,并且由于存在材料消耗的显著问题,激光隐切技术还可实现将碳化硅晶圆的产出率提高30%以上;
(3)特种晶圆切割:采用激光隐切技术对特种晶圆(例如带有芯片贴装薄膜或由低k 材料制成的晶圆)进行切割时,可避免碎裂和裂纹的产生,并实现高效率、高精度的晶圆切割。

图片来源:航天三江激光产业技术研究院
不断进阶的激光隐切技术
尽管激光隐切技术具有诸多优势,但在切割过程中仍会受到一系列问题的干扰。如图4所示,晶圆表面翘曲、激光能量密度调控问题将导致激光焦点无法精确落在晶圆中的具体薄层,阻碍了切割精度、芯片良率的进一步提升;由于激光束在加速、减速和转角段难以均匀作用于晶圆,容易出现过度加工等问题;此外模拟量干扰、模拟量非线性、模拟量零漂,或驱动器电流环延迟等问题,将影响激光切割平台的控制精度和响应度。
图4 (a)晶圆表面翘曲影响切割精度,(b)激光作用不均匀导致过度加工
针对以上问题,目前学术界和产业界提出了一系列的解决方案,如图5所示,具体包括:
(1)实时高度跟随控制:在切割晶圆时,通过位移传感器实时测量产品表面微小的高度波动,并实时补偿到激光器所在的z轴,确保激光焦点精确落在晶圆中的具体薄层;
(2)高速位置比较输出控制:开发高度跟随算法,有效避免了激光在加速、减速和转角段的过度加工问题,使激光均匀地作用在被加工物体上;
(3)PWM(脉冲宽度调制)控制技术:通过控制器直接产出开关量信号,经功率放大模块后直接控制电机电流环,实现更快、更直接地提升激光切割平台的控制精度和响应度。
图5 (a)晶圆激光隐切时采用的高度跟随方案,(b)在运动轨迹的所有阶段以恒定的空间间隔采集高度数据,(c)用开关量信号控制电机电流环
针对单焦点激光隐切的作用面积小、激光作用功率调谐问题,人们还针对性地开发了多焦点激光隐切技术,该技术能够在晶圆内部同时聚焦生成多个焦点进行切割,实现切割效率成倍地提高,如图6所示。
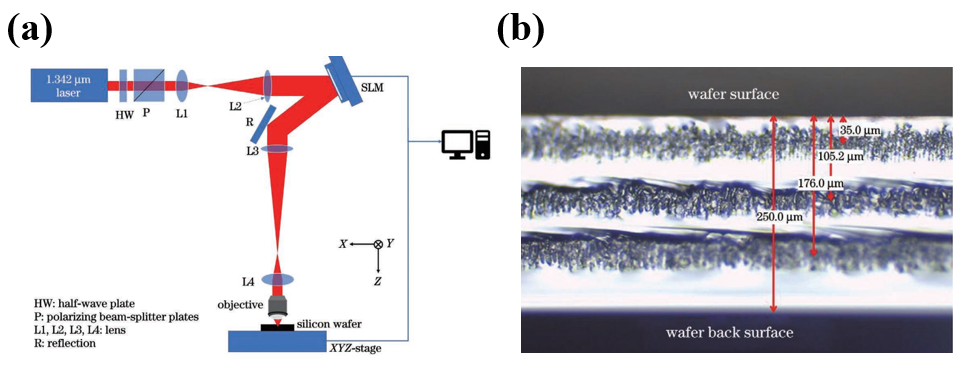
图6 (a)多焦点隐切实验装置原理图,(b)多焦点激光隐切后的晶圆横截面
在多焦点激光隐切过程中,激光束的位置和强度对切割质量都具有较大影响,并且由于空气和半导体材料的折射率差距过大,作用在晶圆内部的激光束会产生焦斑弥散现象,所以需要像差矫正。为了满足不同应用场合下的晶圆切割需求,人们还针对以上问题开展技术攻关,包括调控多焦点的位置和强度,开发像差矫正技术以克服焦斑弥散现象等。
激光隐切技术将有更广阔的天地
激光隐切相对传统的切割技术而言,在实际应用中具有显著的高效率、高质量和低损失等优越性,通过对激光隐切技术进行进一步的优化和探索,例如:通过调节激光隐切过程中的光束能量实现光芯片的表面粗化;进一步提高激光隐切的效率等,我们相信这项技术在集成电路半导体制造以及其他新兴领域中,都将大放异彩。